Sustainability
Sustainability is commonly defined as meeting the needs of the present without compromising the ability of future generations to meet their own needs. At Crane Company, we interpret this concept through the lens of our environmental initiatives, emphasizing the critical relationship between our operations and the environment. This perspective underscores our commitment to minimizing our environmental footprint while contributing to a more sustainable future.
As a responsible corporate citizen, we recognize the importance of reducing our reliance on natural resources and mitigating our environmental impact. Acknowledging that resources are finite, we are committed to addressing the broader risks associated with environmental sustainability – risks that extend beyond our own operations. To that end, the Company has integrated climate-related physical and transition risk factors into the Enterprise Risk Management process conducted annually for all businesses. This ensures that potential climate-related impacts, such as extreme weather events, regulatory changes, and market shifts, are systematically evaluated and addressed as part of our overall risk management framework.
Sustainability is ingrained in our operational philosophy, aligned with our commitment to lean manufacturing and resource efficiency. By establishing clear metrics and tracking progress, we continue to identify new opportunities to enhance environmental stewardship while advancing our business strategy. As part of this commitment, we are actively working toward our 2030 sustainability targets, reinforcing our dedication to long-term environmental sustainability.
2030 Sustainability Targets
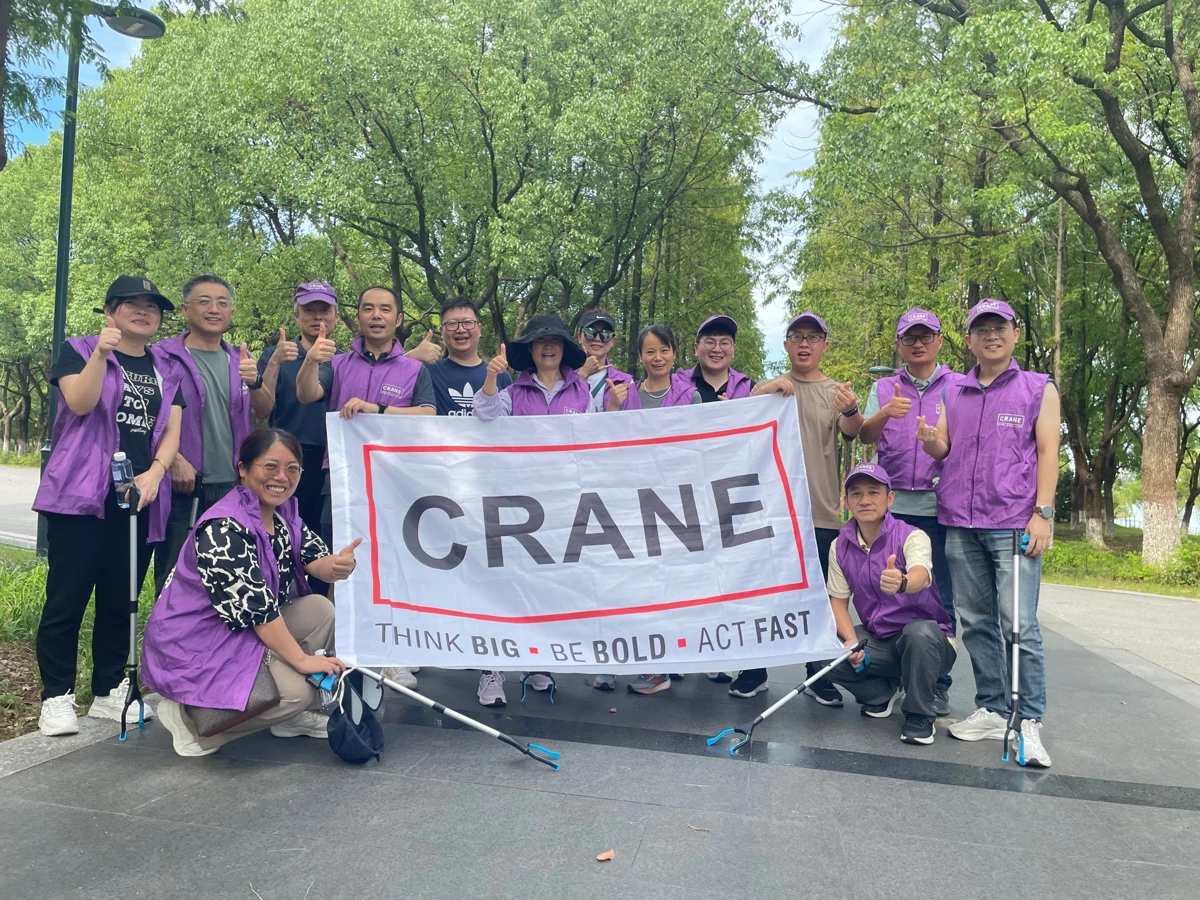
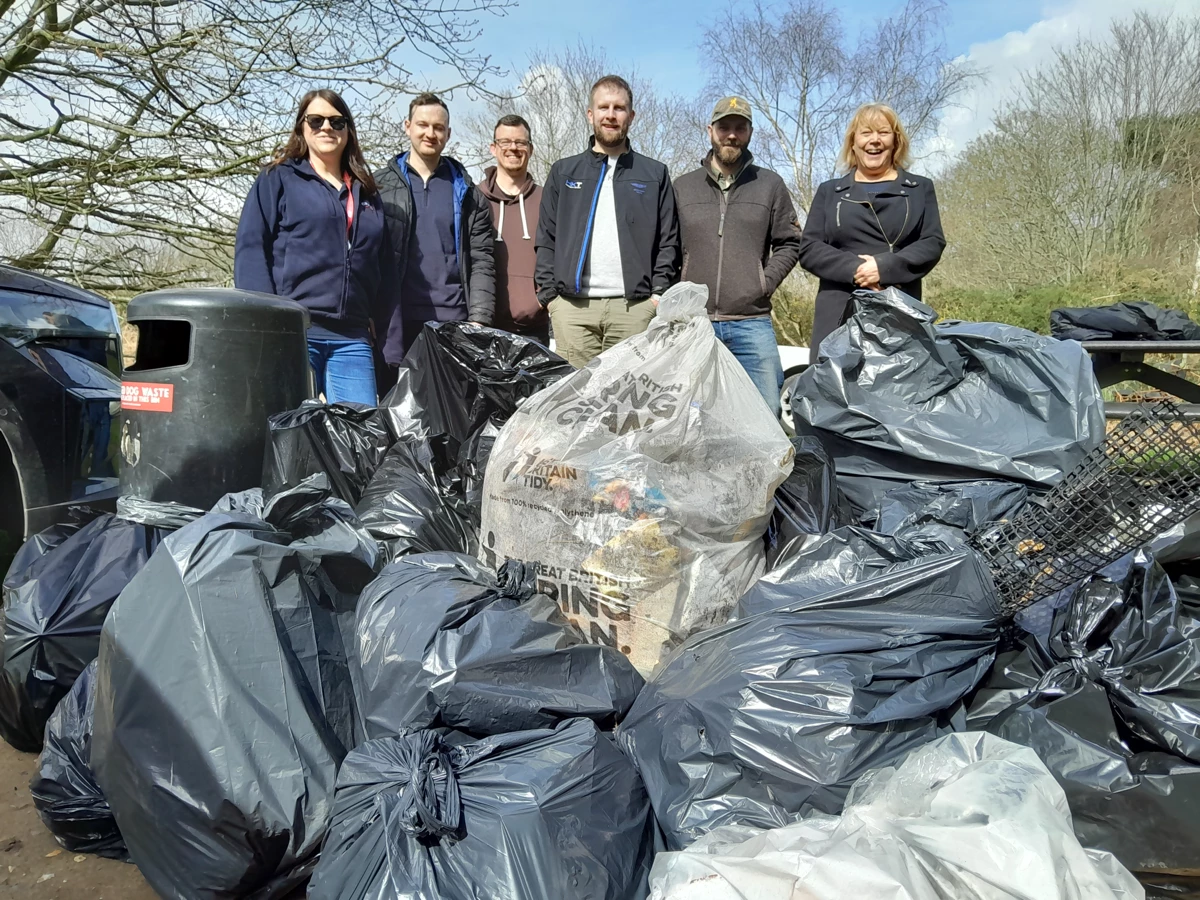
Safety is a #1 Business Priority
57% below the industry average
over two decades
2024 Sustainability Statistics
Electricity Reduction Highlight
Optimizing Production and Reducing Electricity Use with Conformal Coating Innovation
As part of Crane’s ongoing efforts to lower electricity consumption, a new initiative was implemented to optimize the conformal coating process – a critical step in the manufacturing of Crane Aerospace & Electronics’ circuit boards. This project involved transitioning to a new coating material with a significantly shorter drying time, reducing the oven-based process from 20 hours to just 30 minutes. By cutting down drying time by over 97%, the Company alleviates a longstanding production bottleneck and realizes substantial electricity savings by operating ovens for a small fraction of the previous duration.
This initiative built on Crane’s 2023 investment in a new conformal coating machine, which is currently in the programming phase. While not all conformal coating processes have been transitioned to the new machine, progress is steadily advancing. Once fully operational, the combination of the new machine and faster-drying material will allow for smoother workflows, shorter production cycles, and a reduced carbon footprint.
The benefits of this project extend beyond energy savings and production efficiency. It serves as a prime example of how sustainability initiatives can address broader challenges in manufacturing. Material swaps like this are systematically evaluated across the Company’s product lines, with a focus on delivering time, cost, and energy savings. Such changes enhance operational effectiveness while simultaneously reinforcing the Company’s continuous improvement mindset and commitment to responsible manufacturing practices.
As the new conformal coating machine nears full implementation, this project highlights how targeted improvements in materials and processes can drive meaningful progress toward sustainability goals. By combining innovative technologies with thoughtful resource management, Crane continues to demonstrate our ability to adapt and innovate for a more efficient future.
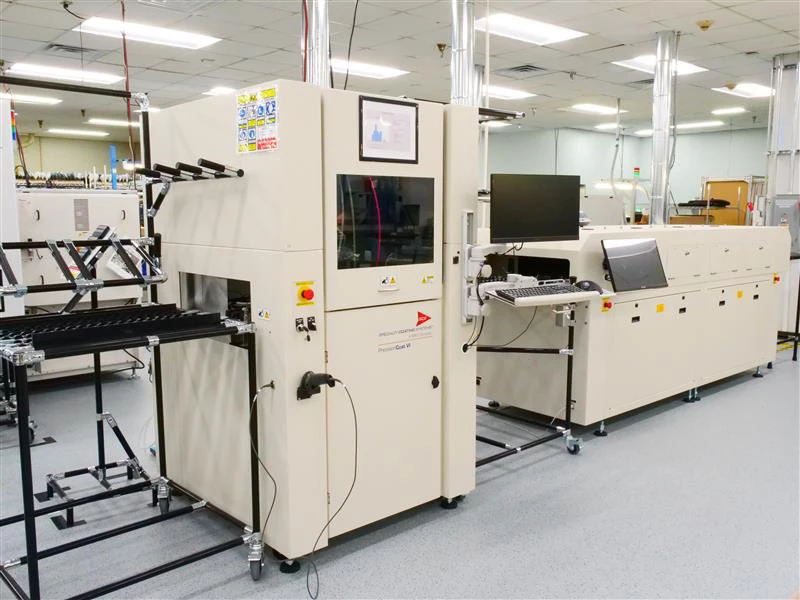